The future is at the core of the best supply chains. But how can a plan made today, foresee tomorrow? Alexandra Leonards reports…
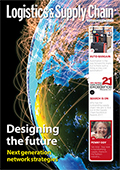
Network design and optimisation is not a one-size-fits-all process. In fact, it’s very subjective – often determined by the size and nature of a supply chain. But its position as an on-going part of a company’s development means getting it right is recognised as critical by all.
Essentially, a network design aims to identify the best way to arrange people, facilities and transport to move goods and services in the most effective way.
“This process can range from being very structured, detailed, and data driven to very ad hoc and intuitive,” says Henry Canitz, director of product marketing at Logility.
Despite the varied nature of networks across the globe, one thing that can be agreed on by all supply chain operators, across all industries, is the importance of looking ahead. With global supply chains changing so rapidly, each year being worlds apart from the next, it’s crucial for networks to position the future at the very core of that design.
“Supply chain network designs should consider future business needs and incorporate capabilities to meet those needs,” says Canitz. “How most companies accomplish this is through long-range strategic planning enabled by long-range forecasts.”
How far a business looks into the future really depends on how fast a business is moving, and how long that business takes to implement supply chain changes. “If it takes five years to build a new distribution centre or manufacturing plant then you need to be looking out at least that far to ensure you can take advantage of potential opportunities and mitigate any potential risks,” says Canitz. “It can be challenging to fully evaluate and redesign a complex supply chain network.
“Any effort will have to incorporate many moving parts and a significant amount of data.”
Without sufficient tools, exploring all the different factors associated with the process is near impossible. “Even if you have dedicated network design tools there can be a learning curve associated with using them,” says Canitz. “In addition, supply chain network design projects are conducted infrequently and, as time passes, the original team may have moved into a different role.
“There is a high potential for mistakes and with them trust in the proposed design can be lost.”
Lucy Larkin, managing director at Accenture’s retail practice, says that networks need to support future business needs, but that accurately predicting these demands is difficult. “Sensitivity analysis is a key tool in the design process to evaluate risk impact of future change, and understand the limitations of the network solution,” she says. “The assumptions about the future are by far the most important, but also the trickiest to define.”
Some of the most significant factors to consider, she says, include: the service level required to the customer, the inbound and outbound transport costs, the product range, the complexity of the market and flexibility for future changes. Of course, different industries will place a different level of weighting on each area.
“A food manufacturing business may focus on stable inbound and outbound bulk transport and warehouse costs, a technology business may be concerned with speed to market of new products, whereas a pure e-commerce company is likely to be more focused on service to an individual and changing offerings,” says Larkin. Although businesses want future predictions to be as detailed as possible, high-level assumptions could actually limit the accuracy of the results.
“Over time, corporate strategies and goals can change as the market changes,” says Dr Tobias Schulz, senior business consultant at Quintiq EMEA.
“An advanced planning solution is flexible enough to not only reflect these changes, but to support what-if scenarios, which allow planners to test plan changes by modelling them first.”
But what happens if these methods aren’t used, and the future is left unknown? For one, the inability to explore these “what-if” scenarios can be costly in terms of reduction in profits or loss of market share. “To remain competitive, it is vital to have an advanced planning solution in place – to help you master the complexity of your operations and leverage the opportunities found in today’s dynamic marketplace,” says Schulz.
Canitz says that the biggest implications for a suboptimal supply chain network design are poor service and high total supply chain costs. “Neither of which are sustainable in today’s competitive marketplace,” says Canitz. “Most companies take a cyclical and iterative approach to supply chain network design.
“Network design reviews take place on a quarterly or yearly basis incorporating new data that might lead to different operational requirements and tweaks to the network.
“With each new network design, iterative changes are made to keep the network aligned with the latest projected needs.”
Choosing the design
Identifying exactly what is needed from a network is paramount; it lays the foundation for the entire design and planning process. Those responsible for the design need to understand both the scope and aims of the network.
“At the strategic level, the network design should be closely aligned with the overall company strategy and goals,” says Quintiq’s Tobias Schulz. “In many cases, it comes down to opening and closing points in your network.”
Canitz says that if a business is merging an acquired supply chain into its current footprint, it’s important to ask the right questions. “Have you reviewed which facilities to open or close, do you understand the flows, are you looking at your company’s long range plans to see if you can support new products, geographies or channels, or new sourcing strategies (overseas versus domestic),” he says. “After the goals are roughly established your current supply chain process, challenges, footprint, and technologies should be evaluated.
“These need to be matched with your strategic goals. The scope of consideration can then be established and a phased design and optimization process agreed upon.”
Just as important is linking of all the different areas within the supply chain to have an integrated and all-encompassing plan. “An emerging best-practice in supply chain planning and optimisation is to integrate and synchronise operational, tactical, and strategic planning and optimisation processes to ensure alignment,” says Canitz. “Most organisation today run completely different processes across these three horizons using different data, systems, and assumptions and involving different sets of people.”
Next, he says, having subject matter experts analyse each area of data is a key consideration, alongside the overall availability of data. “Validation of inputs is key to gaining agreement on outputs,” he says. “Finally, understanding in what form design outputs will be delivered helps in developing a plan of how to operationalize results.”
Who is actually responsible for the overall design? Canitz says that this can range from teams of subject matter experts using dedicated algorithmic optimisation solutions to single individuals using simple tools like spreadsheets and visual maps.
“In a business landscape where change is the norm, the design process should create trust,” says Larkin. “More than ever the data and analytics, machine learning and AI are reinforcing and creating future supply chain models and operations.
“The basic principles of physical logistics are the same – capacity, lead time, throughput, efficiency, performance are here to stay – but the information and tools are now there to help us generate the answers and to respond in kind and develop the supply chain network to meet today’s demanding digital world and that of tomorrow.”
She says that although choosing and trusting a network can be a highly daunting task, standing still and doing nothing will turn a business into a laggard. “Robust testing of the hypothesis and continuous monitoring of business changes is key to ensuring your network is always serving your business well,” she says. “This underlines the importance of selecting the right path, however it’s far better to get it 80 per cent right constantly than 100 per cent wrong.”
Keeping up to date
So how often should supply chain networks be redesigned? Logility’s Henry Canitz, says that it depends on how fast requirements change and how long it takes to implement changes. “For a fresh food manufacturer where a growing season may only last four months in one region and then shift to another region the supply chain network may need to be redesigned every four months,” he says. “For a chemical manufacturer where demand is fairly stable and it takes seven years to build a new refinery it may only be necessary to review the network every couple of years.
“Complexity of the supply chain network (number of facilities, lanes, products, customers, etc.) may also come into effect when determining how often to redesign.”
Accenture’s Lucy Larkin says that the pace of changing markets and services means businesses need to look at network design as a continuous process now. “Whereas previously an exercise carried out once every few years would have sufficed,” she says. “In many cases, physical supply chain and logistics networks will already exist so it is often a matter of why, when, and how these networks are redesigned to meet business requirements.
“There are many highly topical changes happening in businesses now, most of which will impact on the supply chain including inventory, requirements for the physical networks and supporting IT systems.”
Keeping up to date with the latest information is something that Canitz identifies as important, but often overlooked. “In this disconnected planning environment, strategic objectives are rarely translated to operational plans and the latest operational information is rarely considered during strategic planning,” he says. “The most important supply chain network design objectives should reflect the most current information and fully align to company goals and objectives.
“A supply chain planning system of record can enable aligned and synchronized planning across multiple horizons and ensure that the system being used for network design has the latest and cleanest data to simplify and clarify the design process.”
It’s a varied process – approached differently by different companies. “An express delivery company that is focusing on improving their service levels, for example, might decide to open a new facility in a particular location to better guarantee on-time deliveries,” says Quintiq’s Tobias Schulz. “A second company, like a retailer, might focus on improving the location of their consolidation points to reduce their costs.
“The data comes from different levels within the organisation, but the decisions are made by top-level management and the timing is typically every two to three years.”
According to him, the tactical level of planning looks at the mid-term needs for generating correct schedules, and analysing them. He says that this can happen every six months, but can have seasonal exceptions as well. “ One planning choice could be to purchase additional vehicles going from A to B, or delaying deliveries to collect more on each truck,” he says.
Integrating the tactical and strategic
“Driven by the increasing complexity of supply chains and rising customer expectations, organisations are changing their approach to network design and planning – embracing new solutions that leverage optimization technology and advanced analytics,” says Quintiq’s Tobias Schulz. “They are also seeking integration between their strategic network design and their tactical and operational planning.”
According to Logility’s Henry Canitz, new solutions that take advantage of increased computer processing power, to model the end-to-end supply chain at a detailed level, have become more and more commercially available. “These new solutions can be configured to conduct in depth analysis at a facility level or analysis of the entire supply chain,” says Canitz. “Using algorithmic optimization, these advanced solutions provide an optimal answer to complex problems based on a set of supply chain constraints, business objectives, demand and supply projections, and current network data.”
Accenture’s Lucy Larkin agrees: “The use of big data and analytics is now driving decision making. Early adopters are starting to use machine learning and AI to plan and execute their supply chain.”
She says that analytics is now starting to help business understand logistics requirements far more thoroughly, and demand-sensing can put the right action in place to meeting future customer demand levels.
Logility has a number of tools like its Inventory Optimization (IO) and Integrated Business Planning (IBP) which are used to identify and analyse potential opportunities and risks and deliver an optimal answer. “Organisations use these powerful analytic tools to identify and, more importantly, quantify the tactical and strategic opportunities ahead of them,” says Canitz. “Solutions such as Logility’s network Supply Planning (SP) solution play a key role in operationalizing network strategies in a repeatable, low-risk fashion.”
Larkin says that networks need strong IT systems to support supply chain operations. But in today’s digital world the IT systems are creating new options rather than actually being defined by the process. “The ability to use analytics to keep the network structure under constant review is becoming a new standard,” says Larkin. “IT systems and IT strategy is often required to be considered hand in hand with network design.
“The network design process clearly needs to allow for future changes to the supply chain which may include: more sophisticated order management systems (such as Order Orchestration and Order Promising) which can control more diverse stock holding, expectations for the manufacturing location and logistics costs, global dynamics like trade restrictions, fuel costs, new delivery technology, and Growth impacts and opening of new markets.”
However, enabling technology isn’t particularly easy. “Many solutions available in the market lack of the breadth of capability, including deterministic Network Design LP models, to properly account for uncertainties and risk,” he says.